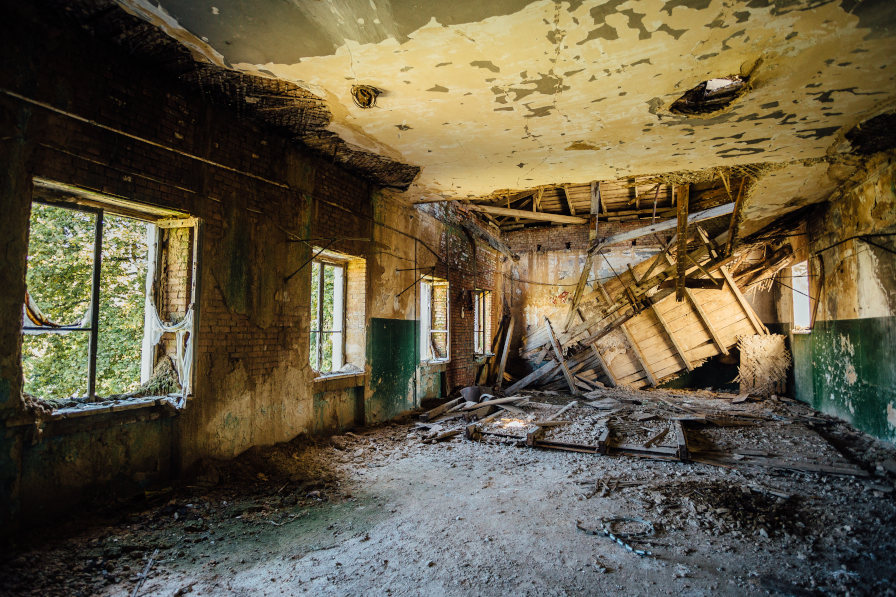

When a commercial lease comes to an end, the process of assessing and claiming dilapidations can often become contentious between landlords and tenants. Dilapidations refer to disrepairs, damages or alterations made without consent that the tenant is liable for rectifying when they vacate the property at the end of the lease term. When presented with a Schedule of Dilapidations, tenants may view the required repairs as unexpected costs and disputes can arise.
As a commercial landlord, it is important to understand your rights under the law regarding who pays or a dilapidation report and the claims process to protect your interests from tenant actions. Having a clear understanding of your legal position can help ensure the dilapidations process goes smoothly.
Understanding Your Rights Regarding Dilapidations
As a commercial landlord in the UK, you have certain key rights when it comes to dilapidations claims that are important to be aware of. First, under the Landlord and Tenant Act 1927, landlords have an automatic right to claim against tenants for any breaches of their repairing obligations or damages to the property. This means you can legally seek compensations for disrepairs or alterations the tenant was responsible for rectifying per the lease agreement.
You also have the right to serve a Schedule of Dilapidations on the tenant during the last 6 months of the lease term. This detailed document will specify all the dilapidations issues that need to be remedied before the lease expires. The tenant is legally obligated to address these dilapidations outlined prior to vacating the premises. As a landlord, it’s advisable to engage a Schedule of Condition at the beginning of a lease to protect yourself and your tenants.
In addition, the 1927 Act grants landlords the right to inspect the property’s condition at any point during the lease term, as long as proper notice is provided to the tenant. This allows you to identify potential dilapidations early on and bring them to the tenant’s attention.
Who Pays for the Dilapidation Report?
A dilapidation report conducted by a surveyor is a key piece of evidence in supporting a landlord’s claim. But who is responsible for covering the cost of this report – the landlord or the tenant? In most cases, it is the landlord who pays for the dilapidation survey report upfront. The cost then gets built into the overall claim against the tenant for compensations.
For a report to be considered impartial evidence, it should be commissioned independently by the landlord rather than jointly. The landlord has a right under property law to inspect the premises during the lease term after giving notice. Therefore, they can commission reports whenever needed. If the claim goes to court and succeeds, the judge may award the reasonable cost of the report back to the landlord as part of the judgement.
While the landlord typically pays upfront, if repairs are deemed the responsibility of the tenant, the cost of an independent dilapidation survey is a recoverable expense through the compensation claim process.
What is the Process for Pursuing Dilapidation Payments?
If a commercial tenant fails to satisfactorily meet the terms of a dilapidations agreement by rectifying disrepairs to the proper standard before vacating the property, the landlord may need to take further steps to recover the costs incurred.
Property lawyers typically advise landlords to conduct a thorough property inspection or have a dilapidations survey carried out before the end of the lease term. This allows time to hopefully resolve any disputes through negotiation rather than resorting to formal legal proceedings, which can be prolonged and expensive for both parties.
If the tenant refuses to willingly compensate the landlord for identified dilapidations issues, the landlord can formally serve a Schedule of Dilapidations prepared by an independent surveyor outlining the breaches of repair obligations. If the disrepairs remain unaddressed when the tenant vacates at lease end, the landlord has the right to enter the property, survey conditions and undertake necessary repairs.
The next step would be for the landlord to send a formal letter demanding the tenant pay the dilapidations costs within a set timeframe. Mediation is also an option before going to trial to reach a settlement.
Taking a Claim to Court
If a commercial tenant refuses to pay for dilapidations after receiving the landlord’s formal demand for compensation, the matter may end up being resolved through the court system. The landlord will need to file a Part 7 claim with the appropriate court based on the property’s location and serve it on the tenant to initiate proceedings.
From there, both parties will go through a process of disclosing all relevant documents, including property reports, correspondence, repair estimates, photos and more. If no settlement agreement can be reached beforehand, the court will set a trial date, and all involved must exchange witness statements and expert evidence prior.
Overall, pursuing a dilapidation claim in court can be time-consuming and complex. Landlords should seek experienced legal help to build the strongest possible case with thorough evidence and preparation.
Dilapidations can be a complicated and often contentious matter that can be notoriously difficult to resolve. This is where our dilapidation surveys can offer real benefits. Our dilapidation surveyors will help identify the areas where damage or alteration to the property has occurred and where tenants are liable for repairs, and provide expert assistance to help with any court cases.
To find out more about commercial dilapidation surveys at Bradley-Mason LLP and how we can help you, contact us today and we will be delighted to answer any queries.
DISCLAIMER: This article is for general information only and not intended as advice. Each project has its own set of unique circumstances, all potential issues should be investigated by a surveyor on a case by case basis before making any decision.
