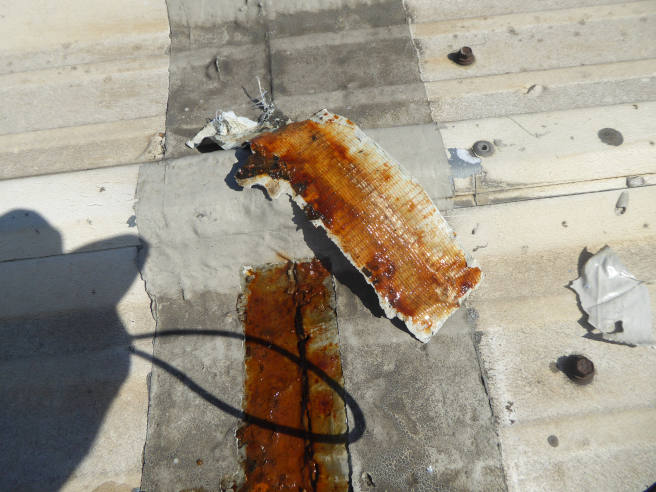

Our commercial roof surveys often identify signs of cut edge corrosion on metal roof cladding. In fact, it’s one of the most common problems on industrial sites, which occurs to metal roofing sheet laps and sheet ends. Cut edge corrosion or CEC looks unsightly but it can also lead to rusting which, if left untreated, can cause irreparable roof leaks and costly roof replacements. For this reason, we strongly recommend dealing with CEC as soon as possible.
What is Cut Edge Corrosion and What Causes It?
Cut edge corrosion is a common issue that affects the metal roofing and siding on commercial buildings. It occurs when the cut edge of a metal sheet is exposed to the elements and begins to corrode over time. Cut edge corrosion typically starts as edge peel at the cut edges of a metal sheet. Pre-finished roof sheeting is cut to size at the manufacturers to fit the building in question, but if the cut edge isn’t weatherproofed, it can leave the material exposed to the elements.
Through natural weathering, this exposed edge can start to corrode. This process then accelerates, particularly at sheet overlaps where rainwater is held by capillary action. The overlapping sheets create a crevice where water can collect and sit stagnant, accelerating corrosion along the cut edge.
Edge corrosion is a progressive problem – left untreated, it can cause the protective coatings on the metal sheets to peel away, revealing the bare metal underneath and allowing further corrosion to take hold. The corrosion can then spread inward from the cut edge, destroying the weather-sealed lap joints and gutter overhangs. This ultimately threatens the waterproofing ability of the roof or siding.
The Impact of Cut Edge Corrosion
Over time, cut edge corrosion can significantly damage metal roofs, cladding, gutters and other metal components of commercial buildings. Left unchecked, it can necessitate full roof or siding replacement, with major financial implications.
On metal roofs, corrosion spreading inward from cut edges can lead to complete failure of the roof sheets and coatings. This allows moisture intrusion, interior damage and ultimately roof collapse which poses health and safety risks and building compliance issues. Replacing an entire commercial metal roof is extremely costly and time-consuming, which can negatively impact your business. Metal cladding on walls is also vulnerable. Corrosion along cut edges can allow moisture penetration behind the cladding, leading to deterioration of the wall structure itself. Damaged cladding must be replaced to restore proper weatherproofing.
In gutters, corrosion typically starts at seams and joints where water accumulates. It can also occur due to galvanic corrosion if different metals are used. Damaged gutters can leak and cause interior water damage. They may need to be partially or fully replaced.
Preventing Cut Edge Corrosion
Routine inspections along cut edges should be performed to look for early signs of corrosion or coating failure, especially in the case of commercial tenancies. Catching and treating cut edge corrosion in early stages can help building owners avoid extensive repairs down the road.
Effective preventative measures include:
- Inspecting metal roofing, cladding and gutters regularly for early signs of corrosion along cut edges or seams. This allows prompt treatment before major damage occurs.
- Applying corrosion-inhibiting sealants or tapes along cut edges and seams during installation. Ensure products used can adhere properly when metal expands and contracts.
- Keeping gutters clean and clear of debris to prevent moisture build up. Check that gutters are properly sloped to drain correctly.
- Replacing damaged or corroded sections of metal roofing to stop deterioration from spreading.
- Consulting roofing and building experts to identify the optimal solutions for preventing and treating cut edge corrosion issues.
Treating Cut Edge Corrosion
Early detection and treatment of cut edge corrosion is highly recommended to prevent costly metal sheet replacement in the future. But it isn’t always possible and once corrosion has set in, treatment is vital. Once cut edge corrosion has taken hold, prompt treatment is required to stop further deterioration. The most effective solutions involve:
- Removal of any loose, flaking metal and corrosion deposits along cut edges and seams. This provides a clean surface for sealants and coatings to adhere to.
- Application of a high-strength, flexible sealant along cut edges and lap joints. The sealant fills in crevices and prevents moisture from accumulating. Flexibility allows it to move with the metal’s expansion and contraction.
- Coating cut edges and damaged areas with a corrosion-inhibiting hybrid coating. This forms an impermeable moisture barrier when added to coatings and provides superior corrosion resistance compared to standard coatings.
- Spot repairs or full replacement of badly corroded sections of metal roofing, gutters or wall panels as needed. This stops deterioration from spreading to adjacent areas.
At Bradley-Mason, we’ve had great results with Sika Liquid Plastics, a tried and tested effective surface treatment for the onset of cut edge corrosion for all commercial properties. Designed to extend the lifespan of the roof surface, sheets remain structurally sound without compromising the waterproofing function.
Here’s a recent before/after example:
Common Mistakes When Treating CEC
Attempting to treat cut edge corrosion without proper training and preparation often leads to failure and recurring issues. Insufficient training on the application of sealants or coatings is a common mistake, which can lead to inadequate corrosion protection.
Likewise, failing to clean and prepare cut edges before applying products can prevent good adhesion. Ensure edges are free of loose metal, rust and other contaminants, and use a primer on rusted areas for better coating bonding. Trying to rush through treatment without dedicating enough time to identify all affected areas, clean thoroughly, apply products correctly and allow proper curing can lead to missed corrosion and product failure.
Seek Professional Expertise
At Bradley-Mason, our team of commercial surveyors have worked with numerous businesses over the years to help them resolve cut edge corrosion on their property. If you would like advice on how to prevent or treat CEC, contact us today.
DISCLAIMER: This article is for general information only and not intended as advice. Each project has its own set of unique circumstances, all potential issues should be investigated by a surveyor on a case by case basis before making any decision.
